Presentation
Normally individuals consider material textures as the normal classification like woven, weaved, meshed or tufted developments. They generally leave Nonwoven Fabrics structure the material gathering. In the regular texture, the fiber is first made into yarns; then again, nonwovens are produced sheets or networks directionally or haphazardly orientated filaments, reinforced through opposition, robustness or staying together into a texture.
The requests for textures have expanded pointedly. Customary materials can’t meet the creation cost and greater expense of upgradation alongside requesting purchasers in new fields of utilization. With better customization of attributes into the texture and propriety to unavoidable end utilizes being benefits, nonwovens have arisen quickly as the textures representing things to come.
Nonwoven Fabrics presents many benefits over ordinary textures, the most clear advantage is cost investment funds. In late two or three years the nonwoven business has arisen at a quick speed, offering a colossal scope of items to china melt blown nonwoven pp meltblown suppliers a few differentiated fields. On the other hand, Nonwoven Fabrics hold a few normal qualities, which drove them to be included for non-usable in specific applications. As of now, many innovative work has been led on improving the qualities of Nonwoven Fabrics. Nonwovens are additionally going into a few shocking fields, with influencing style clothing too.
Right now, three filaments lead the overall market:
Polypropylene (engineered – 63%)
Polyester (engineered – 23%)
Cellulosic staple fiber (regular based 8%)
Fabricating Cycle
To make a nonwoven texture, initial a web is made, and afterward it is tied (reinforced together) to invigorate. Normally, Nonwoven Fabrics are produced using two cycles, a one-step or two-step.
One-step process: In this cycle, the development of web and holding is directed persistently. The cycles, spunbond and soften blown are viewed as under one-step.
Spunbond process: The thermoplastic filaments are expelled through a spinneret, and afterward is it spread on a transport line to make a web. Following the cycle, the web is reinforced by going it through two schedule rollers.
Liquefy blown process: The thermoplastic filaments are driven onto a gatherer screen to make a web. The blend of filaments fixing and trapping, results holding.
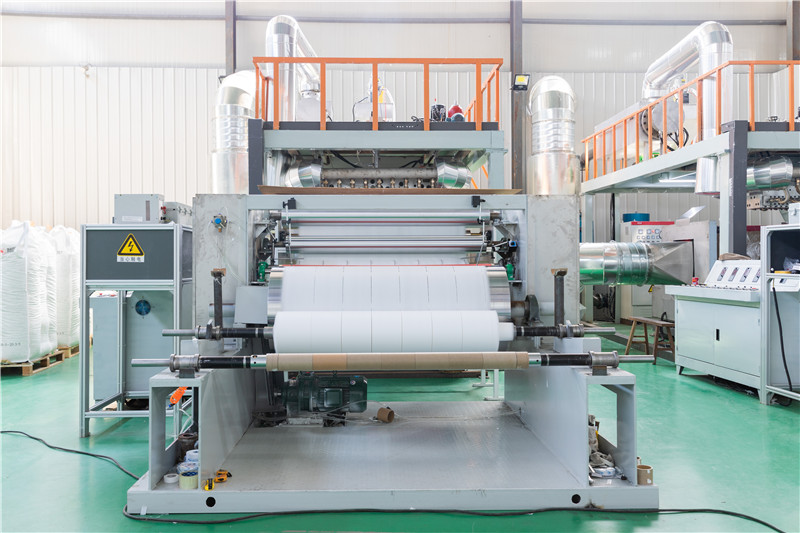