Principle of the indirect axial load measurement method
In the design process of an aero-engine, according to the calculation method of the axial force of the engine rotor, the axial force of the rotor can be divided into two parts: the axial force of the disc cavity and the axial force of the flow channel. The axial force of the disk cavity is the sum of the axial loads on the rotor system of each chamber in the engine air system, and the axial force of the flow channel is the sum of the axial loads on the flow channel of the engine compressor turbine. The calculation of each axial force component by the china high quality ball bearing factory is mainly based on the momentum theorem.
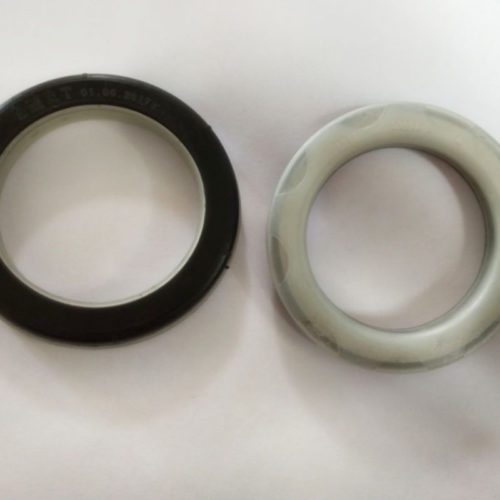
The input parameters for rotor axial force calculation mainly include:
Static pressure, axial velocity, and area at the inlet of the runner, static pressure, axial velocity, and area at the outlet of the runner, mass flow through the runner, disc cavity pressure, geometric parameters of the runner and disc cavity, etc.
The indirect measurement method of the axial load of the ball bearing is proposed based on the calculation method of the axial force of the rotor. The basic idea is to calculate and superimpose the axial force of the disc cavity and the axial force of the flow channel of each component.
For the axial force of the disc cavity, it can be calculated by measuring the cavity pressure of each cavity related to the engine rotor system in real time, combined with the geometric dimensions of the corresponding disc cavity. However, due to the limitation and feasibility of the test system, it is impossible to fully measure the pressure of the air system chamber required by the engine during the engine test run, so relevant calculations must be performed. For example, the pressure of the disc cavity can be estimated through the flow pressure, back pressure and sealing form of the disc cavity, combined with certain empirical formulas and correction methods, and then all the required air can be obtained after relevant calculations and processing. The static pressure of the system disc cavity, so as to realize the real-time measurement and calculation of the axial force of the disc cavity. The key to the calculation lies in the selection of empirical formulas and correction parameters, which directly affect the accuracy of the calculation of the axial force of the disc cavity. When dealing with the axial force of the disk cavity, the influence of the momentum generated by the air flow in the disk cavity on the axial force of the rotor is generally ignored.