The production speed in a diaper machine can be regulated or adjusted through various mechanisms and control systems:
- Variable Speed Drives: Machines often incorporate variable speed drives for motors controlling critical components like conveyors, rollers, or cutting systems. These drives allow operators to adjust the rotational speed, thus regulating the production speed.
- Control Panels and Interfaces: Operators use control panels or interfaces equipped with settings to adjust production speed. These interfaces allow for precise control and modulation of machine speed.
- Automated Control Systems: Advanced machines feature automated control systems that regulate production speed based on predefined parameters or sensor inputs. These systems can adjust speed in real-time to maintain optimal performance.
- Sensor Feedback: Sensors integrated into the production line monitor various factors like material tension, machine load, or product thickness. Feedback from these sensors helps the machine adjust speed to maintain consistent quality.
- Preset Programs and Recipes: Machines may have preset programs or recipes for different production speeds corresponding to specific diaper sizes or designs. Operators can select these presets as needed.
- Synchronized Components: Components of the machine are synchronized to work harmoniously at different speeds. Adjusting the speed of one component often requires corresponding adjustments in other linked components to maintain synchronization.
- Variable Timing Controls: Machines have timing controls for different operations. Adjusting these timings can indirectly impact production speed by altering the duration of specific processes.
- Retrofitting and Upgrades: Some machines allow for retrofitting or upgrades with newer technologies or components that offer enhanced speed control capabilities.
- Safety Considerations: Speed adjustments must consider safety aspects. Machines have safety limits to prevent excessive speeds that could compromise product quality or operator safety.
- Continuous Monitoring and Adjustment: Real-time monitoring of machine performance allows for ongoing adjustments to optimize production speed while ensuring quality standards are maintained.
These mechanisms and control systems provide flexibility in regulating and adjusting the production speed of diaper machines, diaper manufacturer allowing for efficient operation and adaptation to varying production demands.
What measures ensure the safe operation of the diaper machine?
Safety is a paramount concern in the operation of diaper machines. Several measures are implemented to ensure the safe operation of these machines:
- Safety Guards and Enclosures: Machines are equipped with physical guards and enclosures to prevent operator access to moving parts, minimizing the risk of accidents.
- Emergency Stop Buttons: Easily accessible emergency stop buttons halt machine operation instantly in case of emergencies or when immediate intervention is required.
- Interlocking Systems: Safety interlocks are installed to prevent the machine from operating when safety guards or doors are open, ensuring that operators cannot access hazardous areas during operation.
- Safety Sensors: Sensors detect abnormal conditions, such as excessive heat, high pressure, or material jams, triggering automatic shutdowns or alarms to prevent potential hazards.
- Operator Training: Comprehensive training programs ensure that operators are well-versed in machine operation, safety protocols, and emergency procedures.
- Personal Protective Equipment (PPE): Operators are required to wear appropriate PPE like gloves, goggles, or safety shoes to protect themselves during machine operation.
- Regular Maintenance: Scheduled maintenance routines ensure that machines are in optimal condition, reducing the risk of mechanical failures or malfunctions that could pose safety hazards.
- Risk Assessments and Audits: Regular risk assessments and safety audits identify potential hazards and vulnerabilities in machine operation, allowing for corrective actions to be taken proactively.
- Clear Warning Signs and Labels: Machines are labeled with clear warning signs indicating potential hazards or risks associated with specific machine areas or operations.
- Safety Protocols and Procedures: Defined safety protocols and procedures are established for routine operation, maintenance, cleaning, and troubleshooting, ensuring consistent adherence to safety measures.
- Emergency Response Plans: Prepared emergency response plans outline steps to be taken in case of accidents, fires, or other emergencies, ensuring swift and effective responses to mitigate risks.
By incorporating these safety measures and protocols, diaper machine operators and maintenance personnel can work in a safer environment, reducing the likelihood of accidents and ensuring the well-being of individuals involved in the operation and upkeep of these machines.
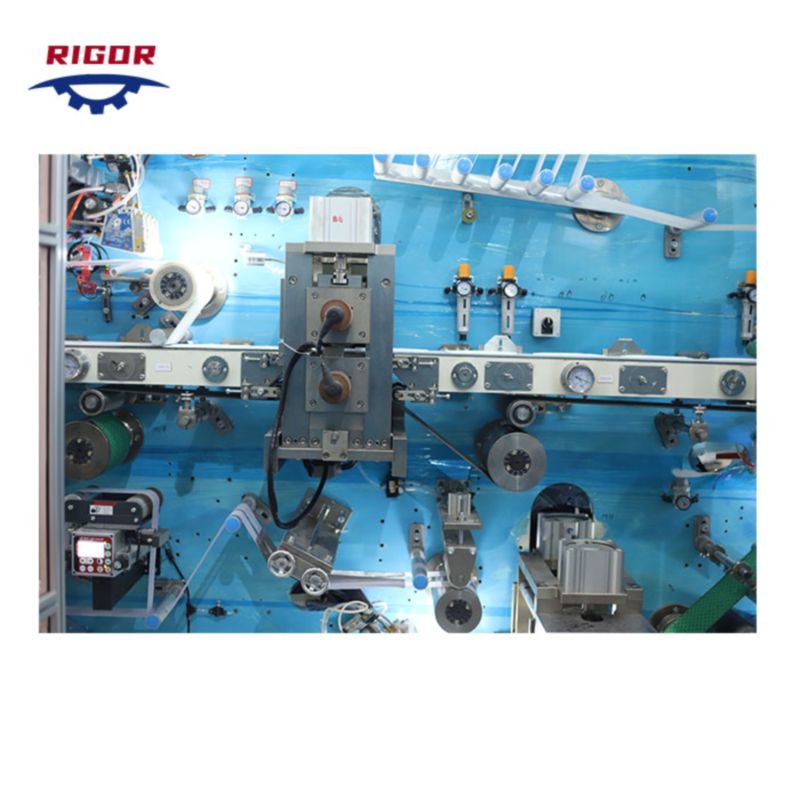